In the industrial landscape, where machinery plays a pivotal role in maintaining operational efficiency, understanding the longevity of equipment becomes crucial. Among these machines, the hose coil wrapping machine stands as a cornerstone in ensuring products are packaged securely and efficiently. Yet, like any mechanical apparatus, these machines require meticulous care to prolong their lifespan.
The transition from neglect to rigorous maintenance not only preserves the machine’s functionality but also optimizes the overall production process. With diverse practices available, it’s vital to pinpoint those that truly make a difference. This article delves into the essential maintenance measures that can dramatically extend the life of a hose coil wrapping machine, offering insights into how businesses can maximize their investment.
Claim: Implementing a robust maintenance strategy is paramount to boosting the efficiency and durability of hose coil wrapping machines, ultimately leading to enhanced productivity and reduced costs.
How Does Regular Inspection Impact Longevity?
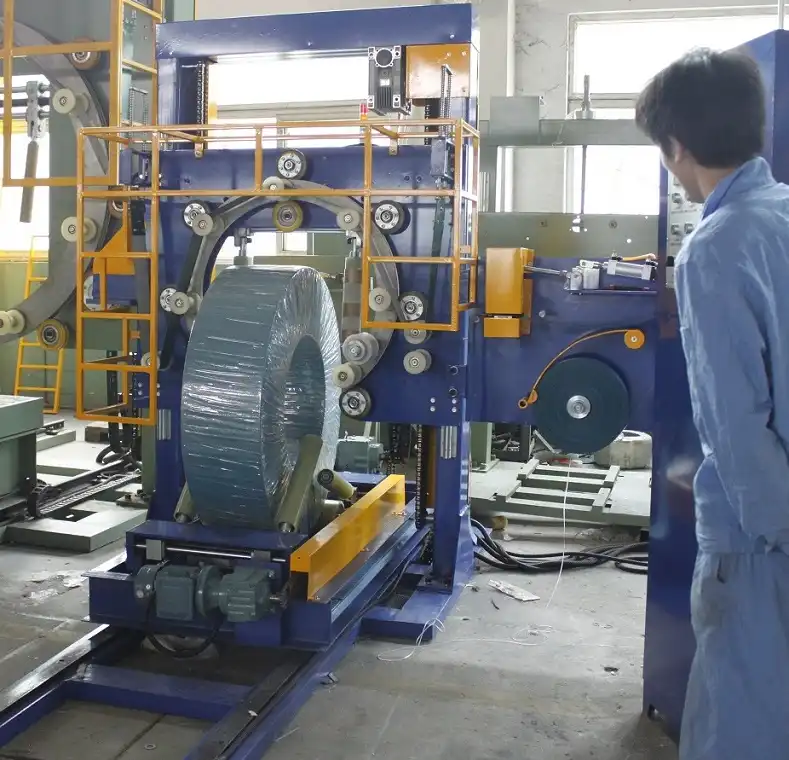
1.1 Understanding the Role of Regular Inspections
Regular inspections serve as the first line of defense against potential malfunctions. By consistently examining the components of a hose coil wrapping machine, operators can identify wear and tear before they escalate into costly repairs. These inspections allow technicians to assess the condition of gears, belts, and other critical parts, ensuring that minor issues are addressed promptly.
1.2 Unveiling the Numbers: The Frequency of Inspections
According to industry standards, machines should undergo a thorough inspection at least once every 500 operating hours. Below is the recommended schedule:
Frequency | Components Checked |
---|---|
Monthly | Belts, Gears |
Quarterly | Electrical Systems |
Annually | Overall System |
1.3 Insights on Preventive Care
Preventive care entails replacing worn-out parts before they fail completely. This proactive approach not only saves money but also minimizes downtime. Machines maintained with routine checks exhibit fewer unexpected breakdowns, which significantly reduces operational disruptions.
1.4 Delving Deeper into Maintenance Techniques
A standard protocol for maintenance includes lubricating moving parts, tightening bolts, and calibrating sensors regularly. Systematic lubrication lowers friction between parts, reducing heat generation and wear. Here’s a deeper look into maintenance scheduling:
Task | Recommended Frequency |
---|---|
Lubrication | Bi-weekly |
Bolt Tightening | Monthly |
Sensor Calibration | Quarterly |
1.5 Two-Fact Statement
True Fact: Regular lubrication can extend the life of a hose coil wrapping machine by up to 30% by reducing friction-related wear.
False Fact: Increasing the machine’s operational speed beyond recommended levels boosts its efficiency and extends its lifespan.
Why Is Operator Training Essential for Machine Maintenance?
2.1 The Importance of Comprehensive Training
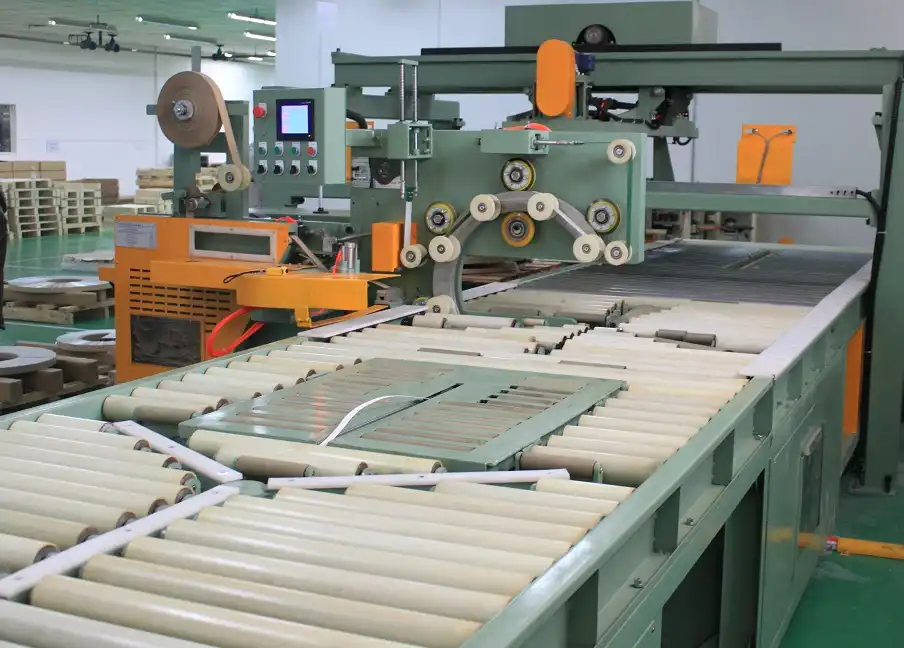
Operator training is fundamental to efficient maintenance. Well-trained personnel can identify irregularities quickly, mitigating possible damage. Training programs focus on teaching operators about the machine’s intricacies, enabling them to perform basic troubleshooting effectively.
2.2 The Impact of Training on Maintenance Effectiveness
Studies show that effective training can reduce maintenance costs by up to 25%. Here’s a brief summary of the advantages of operator training:
Benefit | Percentage Improvement |
---|---|
Reduced Downtime | 15% |
Lower Repair Costs | 10% |
2.3 Detailed Explanation of Training Benefits
Beyond immediate problem-solving, training fosters a culture of maintenance awareness among operators. When personnel understand the critical role of maintenance, they’re more likely to adhere to schedules and report anomalies, thus preventing severe issues from arising.
2.4 Conclusion of Training Insights
Investing in regular training sessions for operators equips them with the knowledge to maintain machines diligently. Training leads to enhanced vigilance, which is crucial for early detection of potential issues. A well-trained team contributes directly to the machine’s extended life and optimal performance.
Conclusion
The practices outlined in this discussion emphasize a strategic approach to maintaining hose coil wrapping machines. Regular inspections, preventive care, and comprehensive operator training form the triad of an effective maintenance regimen. By adhering to these practices, businesses not only prolong the life of their machines but also enhance productivity and reduce costs.
Final Claim: A commitment to structured maintenance and operator education is foundational to maximizing the effectiveness and lifespan of hose coil wrapping machines, securing long-term operational success.