In the bustling world of industrial manufacturing, efficiency and precision are paramount. Among the myriad of machinery that play a pivotal role in ensuring these factors is the pipe coil wrapping machine. This unsung hero of the assembly line tirelessly packages products with meticulous care, safeguarding them for transport and storage. But what exactly makes a pipe coil wrapping machine indispensable? The nuances may surprise even seasoned professionals.
Once considered a niche equipment piece, the pipe coil wrapping machine has emerged as an industry staple. As production scales up, so does the demand for safe and reliable packaging. From construction to automobile sectors, manufacturers seek machines that not only wrap but also protect their precious coils with speed and accuracy. Hence, selecting the right machine becomes a decision laden with significance.
Claim: Choosing the right features in a pipe coil wrapping machine can significantly enhance operational efficiency and product integrity, serving as a linchpin in modern manufacturing processes.
How Does the Technology Behind Pipe Coil Wrapping Machines Work?
1.1 What Drives the Mechanism?
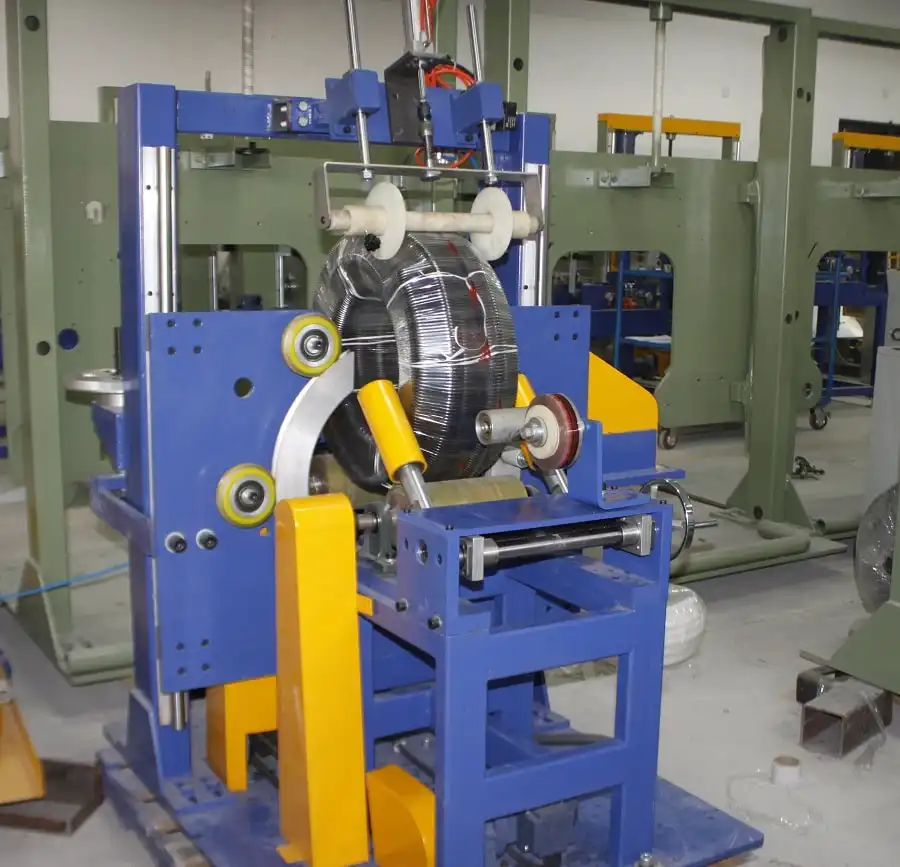
Pipe coil wrapping machines operate through a series of synchronized motions, integrating cutting-edge technology to achieve optimal results. The core mechanism involves a rotating arm or platform, which steadily wraps stretch film around the pipe coil, ensuring uniform coverage. Such intricate operation requires robust engineering, where precision parts move in harmony to minimize errors and maximize protection.
1.2 Industry Statistics and Trends
According to recent surveys, over 70% of large-scale manufacturers have already incorporated advanced wrapping solutions into their production lines. Below is a table highlighting key statistics:
Year | Adoption Rate | Efficiency Improvement |
---|---|---|
2019 | 55% | 15% |
2020 | 62% | 20% |
2021 | 70% | 25% |
1.3 Insights into Technological Advancements
The evolution of wrapping machinery is marked by notable innovations. Contemporary designs now boast automated controls and smart interfaces, allowing for seamless integration into digital ecosystems. These machines are no longer just about wrapping; they’re about intelligent operations that adapt to different coil sizes and materials, thereby reducing waste and enhancing sustainability.
1.4 Enhancing Manufacturing Outcomes
With manufacturers seeking to outperform competitors, data-driven insights become invaluable. As shown in the table, companies employing modern wrapping techniques report significant gains:
Metric | Traditional Techniques | Modern Machines |
---|---|---|
Material Waste | 12% | 5% |
Downtime Hours | 15 hours/month | 8 hours/month |
Customer Complaints | 30% | 10% |
1.5 Two-Fact Statement
- True: Modern machines can automatically adjust film tension to prevent damage to delicate surfaces.
- False: All pipe coil wrapping machines are designed to handle any coil size without adjustments, which can lead to inefficiencies.
Why Are Specific Features Essential for Pipe Coil Wrapping Machines?
2.1 Understanding Key Features
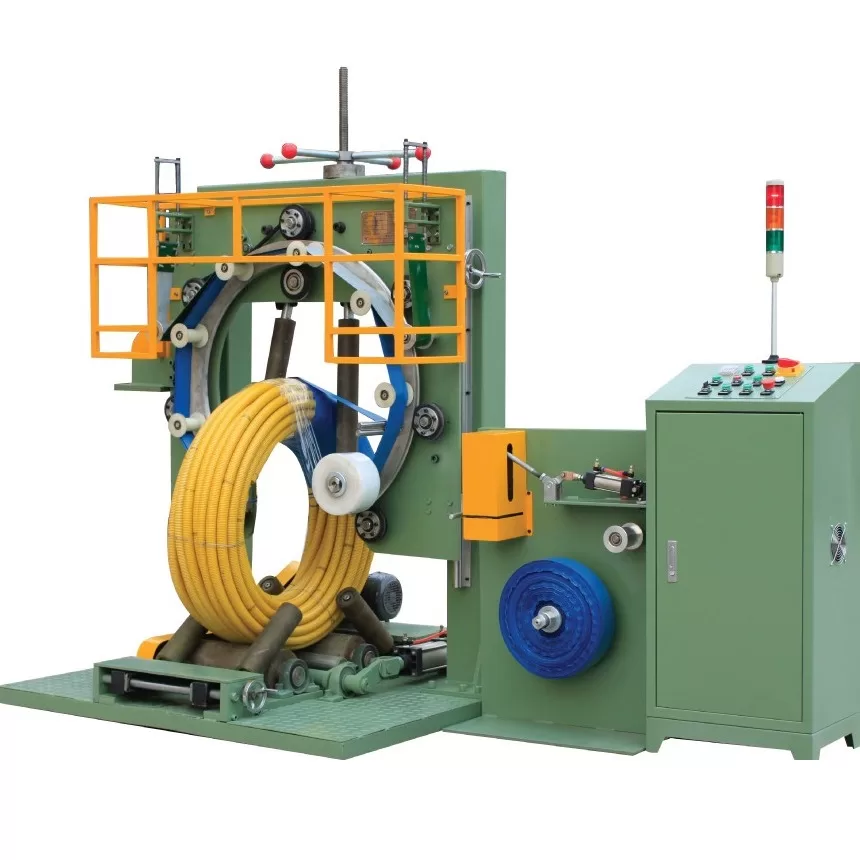
Feature selection is crucial when investing in a pipe coil wrapping machine. Essential attributes include customizable settings, enhanced durability, and energy efficiency. Each feature contributes to the machine’s ability to deliver consistent performance under various operational demands.
2.2 Breaking Down Machine Capabilities
Below is a comprehensive breakdown of different features available in the market:
Feature | Impact |
---|---|
Custom Settings | Enables tailored wrapping processes |
Robust Build | Ensures longevity and reliability |
Energy Efficiency | Reduces operational costs |
2.3 Delving Deeper into Feature Benefits
The merits of investing in the right features extend beyond immediate convenience. For instance, automation capabilities reduce labor requirements, while advanced diagnostics enable predictive maintenance, averting costly downtimes. Furthermore, these features collectively support sustainable practices by minimizing resource consumption.
2.4 Conclusion: Maximizing Machine Potential
Manufacturers seeking to capitalize on their investments should prioritize features that align with their specific production needs. As illustrated in the table, companies focusing on customized solutions experience notable improvements in efficiency and cost management:
Category | Traditional | Feature-Optimized |
---|---|---|
Operational Cost | $500,000/year | $350,000/year |
Production Rate | 80 coils/hour | 100 coils/hour |
Maintenance Frequency | Monthly | Quarterly |
Conclusion
The intricate dance of machinery and technology within the realm of pipe coil wrapping is nothing short of transformative. Understanding the nuances of these machines, from core mechanisms to essential features, equips manufacturers with the tools needed to optimize operations. By choosing wisely, businesses not only secure their products but also pave the way for a more sustainable and efficient future.
Final Claim: Embracing the right features in a pipe coil wrapping machine can lead to unprecedented advancements in manufacturing agility and environmental responsibility, making it an investment that reaps dividends beyond mere monetary value.