In the intricate world of electronics, the wire wrapping machine stands as an unsung hero, pivotal in the assembly of complex circuits. As engineers and technicians delve deeper into the vast sea of electronic components, the necessity for precision and reliability becomes paramount. Wire wrapping machines offer just that, providing a seamless and efficient method to interconnect these components with accuracy and speed.
While the market is flooded with various models and brands, discerning the right wire wrapping machine is not as simple as it seems. From the novice hobbyist to the seasoned professional, understanding the nuances of each machine’s features can significantly impact the quality and efficiency of the work produced. This exploration aims to unravel these features, offering clarity in a sea of technical specifications.
Claim: The right wire wrapping machine can dramatically enhance both productivity and precision, making it an indispensable tool in modern electronics assembly.
Sub-section 1: Why is Wire Wrapping Important in Electronics?
1.1 What makes wire wrapping a preferred technique?
Wire wrapping is cherished for its robustness and reliability. Unlike soldering, which involves melting metal to create connections, wire wrapping uses mechanical force to create a gas-tight connection. This technique ensures that the connections are strong, durable, and resistant to environmental factors such as humidity and vibration. The precision of wire wrapping also allows for easy modifications, making it a favorite in prototype development and repairs.
1.2 How do different machines compare in terms of features?
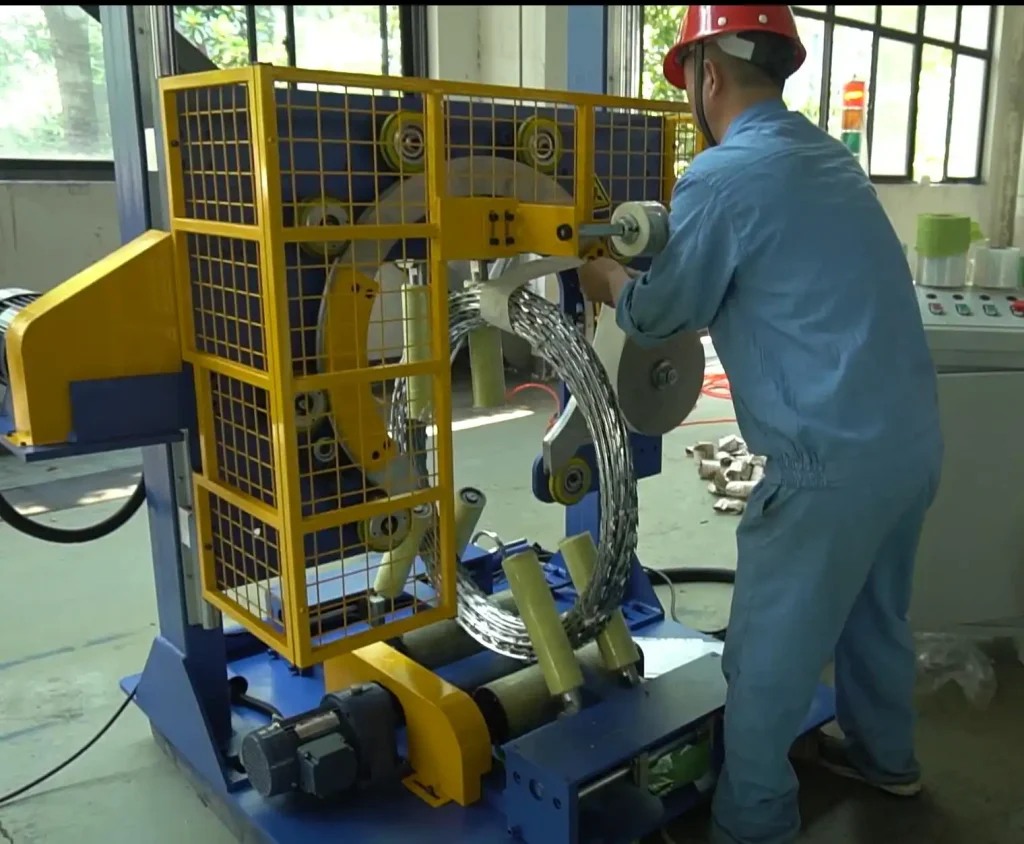
When assessing wire wrapping machines, a variety of features come into play. Here’s a comparative table illustrating some key differentiators:
Feature | Machine A | Machine B | Machine C |
---|---|---|---|
Speed (wraps/min) | 120 | 100 | 150 |
Wire Gauge | 22-30 | 24-32 | 20-28 |
Automation Level | High | Medium | Low |
1.3 How can one choose the right machine based on these features?
Choosing the right machine involves evaluating both the current and future needs of your projects. Consider the wrap speed required for your production scale, the wire gauge compatibility with your components, and the level of automation that will benefit your workflow. Balancing these aspects with the budget constraints is key to making a well-informed decision. A machine that offers versatility in wire gauge and high-speed wrapping can be a game-changer for large-scale projects.
1.4 How do additional features enhance functionality?
Additional features such as tension control, adjustable wrap depth, and ergonomic design can significantly enhance a machine’s functionality. These features allow for greater control and precision in the wrapping process, reducing errors and improving efficiency. Machines with programmable settings can further streamline work, saving time on repetitive tasks and ensuring consistent quality. Here’s a closer look with a table of additional features:
Feature | Benefit |
---|---|
Tension Control | Prevents wire breakage and ensures a tight wrap |
Adjustable Wrap Depth | Allows for customization based on component requirements |
Ergonomic Design | Reduces user fatigue during prolonged use |
1.5 What are some common misconceptions about wire wrapping machines?
Fact 1 (True): Wire wrapping is more reliable than soldering in high-vibration environments due to its mechanical connections.
Fact 2 (False): All wire wrapping machines require extensive maintenance. In reality, many modern machines are designed for minimal upkeep, with features to reduce wear and tear.
Sub-section 2: How Do Advanced Features Influence Performance?
2.1 What role do advanced features play in wire wrapping machines?
Advanced features in wire wrapping machines not only enhance performance but also contribute to greater flexibility and productivity. Features like programmable controls, memory settings for recurring tasks, and compatibility with different wire types allow users to optimize their operations. In high-demand environments, these features can make a significant difference in output quality and consistency.
2.2 Can advanced features justify higher costs?
Advanced features often come at a premium, but their benefits can outweigh the initial costs. Consider the data in the table below:
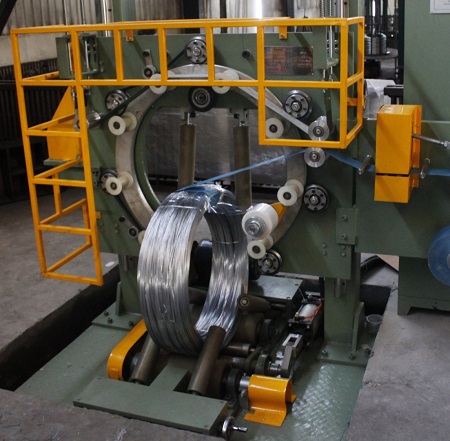
Feature Cost | Benefit |
---|---|
$500 | Increased automation saves 20% in labor costs |
$300 | Improved accuracy reduces errors by 15% |
2.3 How do these features affect long-term efficiency?
In the long term, advanced features contribute to significant efficiency gains. Automation and programmable settings reduce manual intervention, allowing technicians to focus on quality control and other valuable tasks. Additionally, the precision offered by these features minimizes material waste and rework, leading to cost savings and faster turnaround times.
2.4 Conclusion on the impact of advanced features
Advanced features undeniably improve the overall performance and value of wire wrapping machines. By investing in machines with these capabilities, users can experience long-term benefits such as consistent quality, reduced operational costs, and greater flexibility in handling diverse projects. The following table summarizes key insights:
Insight | Impact |
---|---|
Automation | Efficient workflow and reduced errors |
Programmability | Customization for varied projects |
Precision | Improved product quality |
Conclusion
In the fast-evolving realm of electronics, selecting the right wire wrapping machine is crucial for ensuring productivity and precision. By considering key features and advanced capabilities, one can make informed decisions that enhance both current projects and future endeavors. The integration of advanced features not only justifies the investment but also lays the groundwork for sustained operational excellence.
Claim: Investing in a feature-rich wire wrapping machine is not just a purchase, but a strategic decision that promises long-term gains in efficiency, quality, and adaptability.