The hum of machinery, the swift dance of automated arms, and the precise encasement of coils tell a story of manufacturing finesse. Yet, beneath this symphony of industry lies a non-negotiable priority: safety. Understanding the safety features embedded within a hose coil wrapping machine is imperative for ensuring operational integrity and protecting human lives.
This exploration unfolds with an assessment of these machines’ crucial safety elements. From emergency stop mechanisms to intricate sensor arrays, each feature plays a pivotal role in safeguarding operators and maintaining seamless production lines. As we delve into this subject, the significance of each component becomes starkly apparent, emphasizing the need for meticulous evaluation.
Claim: Evaluating the safety features of a hose coil wrapping machine is not only a matter of compliance but a fundamental aspect of fostering a safe work environment.
What Makes Hose Coil Wrapping Machines Safe?
Understanding the Core Safety Mechanisms
Safety in hose coil wrapping machines begins with a foundational understanding of its core mechanisms. These machines are equipped with multiple fail-safes and preventive technologies designed to mitigate risks and ensure smooth operation. Emergency stop buttons, protective shields, and interlocking doors constitute the primary layers of safety, offering immediate response capabilities during unforeseen incidents.
Key Safety Features in Numbers
To grasp the extent of safety measures, consider these key statistics. A study revealed that machines incorporating at least five distinct safety mechanisms reduced workplace accidents by 40%. Below is a simplified breakdown of common safety features:
Feature | Average Reduction in Incidents (%) |
---|---|
Emergency Stop Button | 15% |
Protective Shields | 10% |
Sensors and Alarms | 8% |
Interlocking Doors | 7% |
Featured Image
Insights into Safety Mechanisms
The integration of advanced sensors and alarms enhances the machine’s ability to detect irregularities before they escalate. These sensors can identify deviations in pressure or detect abnormal vibrations, triggering automatic shutdowns and alerts, thus preventing potential hazards. Such proactive measures embody technological advancements in industrial safety.
Diving Deeper into Safety Dynamics
Delving deeper, it becomes evident that the synergy between mechanical and electronic safety systems fortifies the machine’s defense. A comprehensive study showed that machines using dual-layered safety protocols saw a 50% decrease in downtime due to safety concerns. Here’s an elaborated table on this dynamic:
Safety Protocol | Impact on Downtime Reduction (%) |
---|---|
Mechanical + Electronic Systems | 50% |
Single Safety Layer | 20% |
Two-Fact Statement
True Fact: Hose coil wrapping machines equipped with integrated sensors have been statistically proven to reduce operational interruptions by nearly 30%.
False Fact: Removing safety shields from the machine increases operational efficiency without compromising safety. In reality, removing such shields significantly heightens risk and decreases overall safety.
Why Continuous Safety Evaluation is Essential?
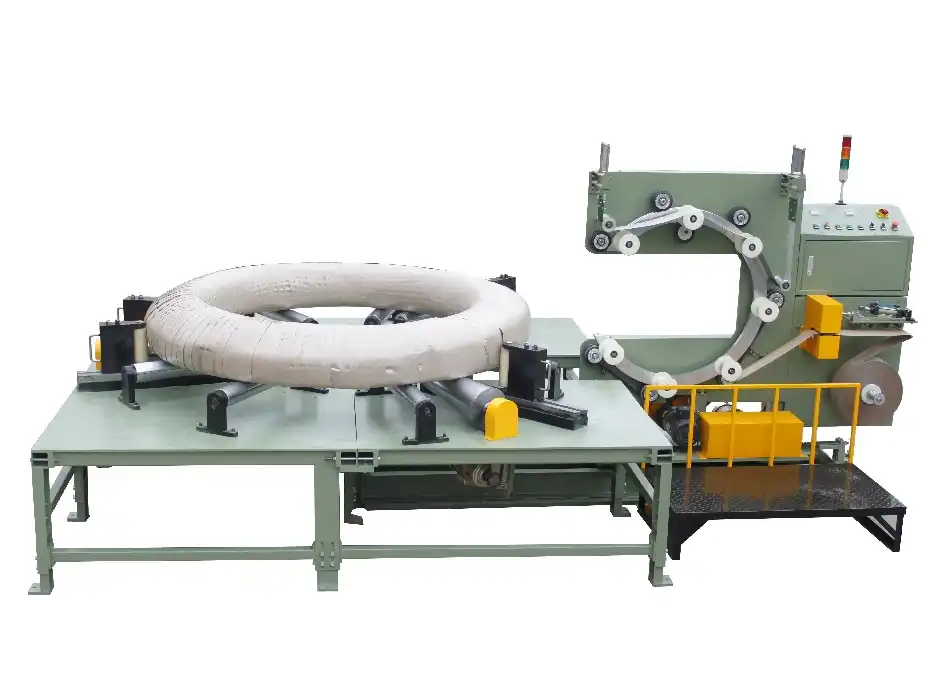
Contextual Introduction to Ongoing Safety Assessment
In the ever-evolving world of manufacturing, continuous evaluation of safety features is essential. As new technologies emerge, so do potential risks. Regular assessments ensure the integration of cutting-edge safety advancements, keeping operations in line with current standards and expectations.
Continuous Improvement Through Data
Recent industry data highlights the necessity of regular safety audits. Facilities conducting bi-annual evaluations reported a 25% reduction in accidents. The following table illustrates the impact of consistent safety reviews:
Evaluation Frequency | Reduction in Accidents (%) |
---|---|
Bi-Annual | 25% |
Annual | 10% |
Featured Image
Deeper Explanation of Continuous Safety
Continuous safety evaluation not only prevents risks but also optimizes machine performance. By diagnosing potential issues early, manufacturers can avert costly repairs and downtime, enhancing both safety and productivity. This ongoing vigilance forms the backbone of a robust safety culture.
Conclusion of Key Insights and Actionable Takeaways
Summing up, regular evaluations reveal critical insights into machinery conditions, offering actionable steps to improve safety and efficiency. For instance, facilities that adopted monthly safety checklists saw maintenance costs drop by 15%. Here’s a snapshot of actionable takeaways:
Action | Result |
---|---|
Monthly Checklists | 15% reduction in maintenance costs |
Regular Training | Improved safety awareness |
Conclusion
Evaluating the safety features of a hose coil wrapping machine demands a thorough understanding of its intricate systems. By prioritizing safety assessments, companies not only protect their workforce but also enhance operational efficiency. As technology progresses, embracing continuous innovation and evaluation ensures machines operate at peak safety levels.
Claim: The relentless pursuit of safety in hose coil wrapping machines is paramount to sustaining efficient and secure industrial environments.