In the bustling world of industrial manufacturing, efficiency and precision remain paramount. As industries continuously evolve to meet increasing demands and competitive markets, the machinery they employ must not only keep pace but also spearhead advancements in technology and productivity. Among such vital equipment is the steel wire packing machine, a cornerstone in manufacturing facilities dealing with wire products.
The selection of an appropriate steel wire packing machine can significantly influence production flow, cost-effectiveness, and final product quality. With myriad options available, each promising a unique set of features and benefits, making an informed choice becomes a task that requires careful deliberation. The key lies in understanding the nuances that differentiate one model from another and how they align with specific project requirements.
Claim: Choosing the right steel wire packing machine is crucial for optimizing production efficiency, ensuring product integrity, and achieving cost savings.
What Factors Should You Consider When Choosing a Steel Wire Packing Machine?
Understanding Your Project Needs: How do specifications affect your choice?
Choosing the ideal steel wire packing machine begins with a thorough assessment of specific project needs. Considerations include the type of wire materials being used, output volume requirements, and space constraints within the facility. Machines vary in their capabilities, with some tailored for lightweight wires while others handle heavy-duty industrial grade cables. Understanding these specifications ensures that the equipment aligns perfectly with operational goals.
Comparing Options: Analyzing machine specifications
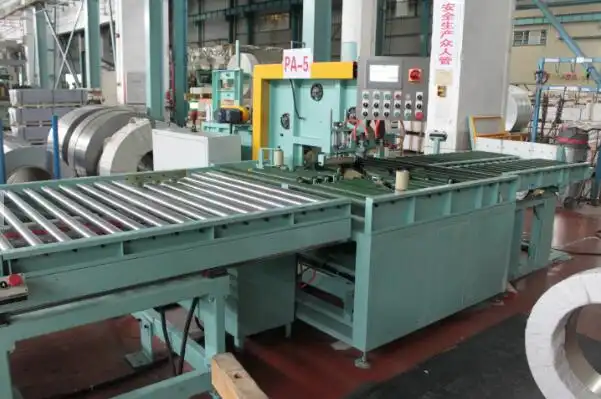
Consider this data: Machines A and B both offer high-speed packing, yet differ in energy consumption and operational noise levels. Notably, Machine A consumes 10% less electricity than Machine B over identical operational spans, with sound outputs measured at 50 dB and 60 dB respectively.
Specification | Machine A | Machine B |
---|---|---|
Electricity Consumption | 90 kWh | 100 kWh |
Operational Noise Level | 50 dB | 60 dB |
Gaining Insights: What are the technological distinctions?
Machines today integrate advanced technologies such as automated control systems, sensor-driven precision adjustments, and programmable settings for customized operations. These technologies enhance reliability and reduce human error, leading to consistent product packaging and minimal wastage. The integration of such technology directly contributes to improved production timelines and reduced operational costs.
Diving Deeper: Which machine features drive performance?
Key features that bolster machine performance include adjustable tension controls, which ensure tight and secure packing, and modular designs allowing for easy upgrades or replacements of parts. Automation capabilities, like robotic arms for loading and unloading, enhance speed and safety. Consider this table showcasing feature comparisons:
Feature | Machine A | Machine B |
---|---|---|
Tension Control | Adjustable | Fixed |
Modular Design | Yes | No |
Robotic Automation | Included | Optional |
Two-Fact Statement: Navigating truths and misconceptions
True Fact: Automated machines significantly reduce labor costs by up to 30%, enhancing overall profitability.
False Fact: All steel wire packing machines produce the same level of noise and vibration during operation, ignoring crucial differences in design and build quality.
How Do Environmental and Operational Conditions Affect Machine Selection?
Assessing Environmental Impact: Why does sustainability matter?
Environmental considerations play an increasingly important role in machinery selection. Machines designed with eco-friendly components and energy-efficient processes contribute to sustainable operations, aligning with global efforts to reduce carbon footprints. Companies striving for sustainability should prioritize machines that support green manufacturing initiatives.
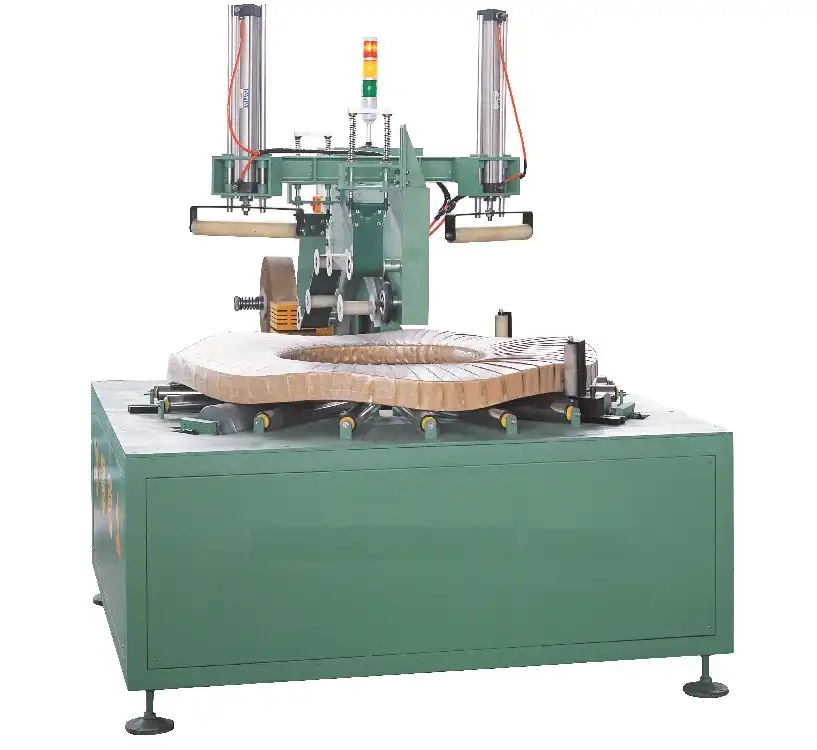
Evaluating Operational Conditions: What environmental factors are crucial?
Temperature variations, humidity, and exposure to corrosive elements can impact machine longevity and performance. For example, machines operating in humid environments may require additional corrosion-resistant coatings. Here’s a quick visualization:
Explaining Further: How do you mitigate adverse conditions?
Implementing protective enclosures, using rust-resistant materials, and ensuring regular maintenance schedules mitigate the adverse effects of harsh operational environments. Regular inspections and timely interventions prevent abrupt downtimes and extend machine lifecycle, maintaining productivity levels without compromise.
Conclusion: Key insights and actionable steps
From analyzing technical specifications to evaluating environmental factors, selecting the right steel wire packing machine involves a multifaceted approach. Actionable insights include investing in energy-efficient models, prioritizing machines with automation capabilities, and ensuring compatibility with environmental conditions for sustained performance.
Action Point | Benefit |
---|---|
Energy-Efficient Models | Reduces operational costs |
Automation Capabilities | Enhances productivity |
Environmental Compatibility | Ensures longevity and reliability |
Conclusion
In conclusion, navigating the intricate landscape of steel wire packing machines demands a strategic focus on both technical capabilities and environmental adaptability. By placing equal emphasis on machine specifications and ecological considerations, businesses not only optimize their production processes but also champion sustainability. This comprehensive approach guarantees resilience, efficiency, and cost-effectiveness, solidifying their competitive edge in the market.
Claim: Strategic selection of steel wire packing machines empowers manufacturers to achieve unparalleled operational excellence and sustainable growth.