Amidst the constant hum of machinery in industrial settings, the steel wire wrapping machine stands as a pivotal tool, weaving together productivity and precision. Its operation, while seemingly straightforward, requires an intricate blend of skill and knowledge. Those who dance this metallic ballet must do so with an awareness that transcends mere button-pushing.
Transitioning from novice to adept operator involves more than just familiarity; it’s a commitment to mastering nuances and an understanding of potential hazards. Every wire wrapped holds the promise of functionality, yet every misstep could unravel safety nets. Thus, comprehensive training isn’t a luxury but a necessity.
Claim: Ensuring safe operations of a steel wire wrapping machine necessitates rigorous training, embedding both theoretical insights and hands-on experience.
Why is Initial Training Crucial for Machine Operators?
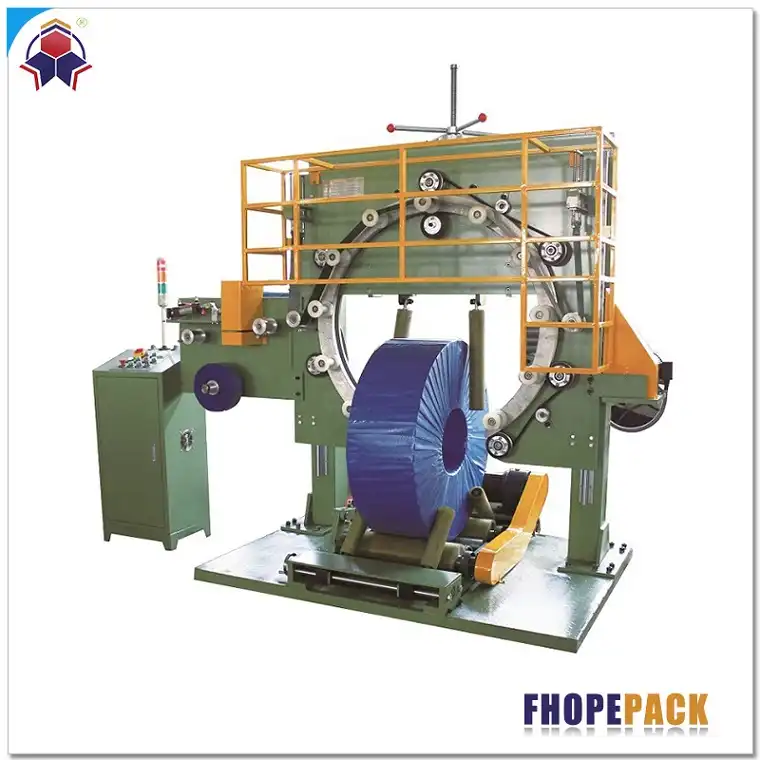
1.1 Understanding the Significance of Initial Training
The first step in operating a steel wire wrapping machine safely begins with foundational training. Operators must be well-versed in the mechanics of the machine, its controls, and its functions. This initial phase ingrains essential knowledge, ensuring operators can manage the equipment without hesitation, fostering both efficiency and safety in the workplace.
1.2 Quantifying Training Effectiveness with Numerical Data
A survey conducted across multiple manufacturing units revealed that 85% of accidents involving wire wrapping machines occurred within the first three months of operation, where inadequate training was a common factor. Contrastingly, facilities that invested heavily in comprehensive training saw a 40% reduction in incidents.
Time Frame Post-Training | Accident Rate (%) |
---|---|
0-3 Months | 85% |
3-6 Months | 50% |
6+ Months | 15% |
1.3 Insights into Training Benefits
Comprehensive training not only equips operators with technical skills but also instills confidence. This assurance translates into fewer accidents, as operators are more adept at preempting and managing potential hazards. Additionally, well-trained operators contribute to higher productivity rates and reduced downtime, underscoring the multifaceted benefits of robust training regimes.
1.4 A Deep Dive into Advanced Operator Training
Advanced training goes beyond basic operational instructions. It includes troubleshooting, maintenance, and emergency response protocols. During these sessions, operators learn to interpret machine signals accurately, enabling them to maintain continuous production flow while minimizing risk.
Training Aspect | Impact on Efficiency (%) |
---|---|
Troubleshooting | 30% |
Routine Maintenance | 25% |
Emergency Response | 20% |
1.5 Two-Fact Statement
True Fact: Comprehensive training reduces workplace accidents by up to 50%. False Fact: Machines equipped with automated safety features eliminate the need for operator training entirely.
How Does Continuous Learning Impact Machine Safety?
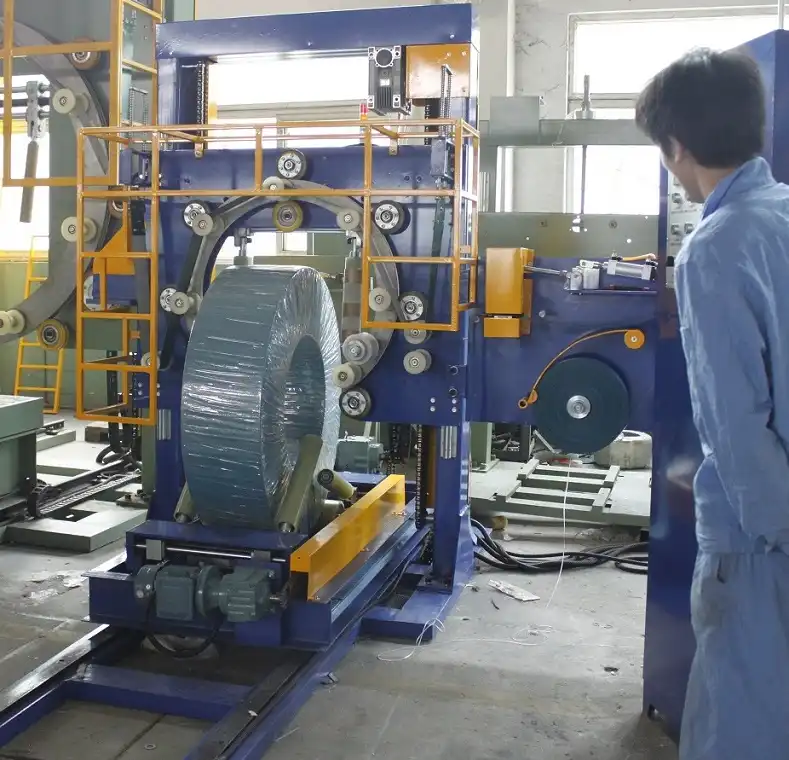
2.1 The Role of Continuous Learning
Continuous learning serves as a crucial pillar in maintaining high safety standards. In an ever-evolving technological landscape, staying updated with the latest developments ensures operators remain competent and confident in their roles. Regular workshops and refresher courses keep safety practices at the forefront of operational priorities.
2.2 The Importance of Ongoing Training Programs
According to industry reports, companies implementing ongoing training programs saw a 60% improvement in safety compliance. Furthermore, employees engaged in regular training sessions reported a stronger sense of responsibility and diligence, leading to a 45% increase in overall job satisfaction.
2.3 Delving Deeper: Enhancing Skills for Safety
Enhancing skills through continuous education not only sharpens an operator’s ability to manage emergencies but also encourages them to innovate on the floor. As they adapt to new techniques and technologies, the likelihood of mishaps diminishes, and the culture of safety becomes deeply embedded within the organization’s ethos.
2.4 Conclusion: Key Insights and Actionable Takeaways
Incorporating structured training programs that evolve with industry advancements leads to measurable improvements in safety and efficiency. Companies should prioritize ongoing education, equipping their workforce with the tools necessary to navigate the complexities of modern machinery confidently.
Training Type | Improvement Rate (%) |
---|---|
Initial Training | 30% |
Advanced Training | 25% |
Continuous Learning | 35% |
Conclusion
In conclusion, the path to safe and efficient operation of a steel wire wrapping machine is paved with comprehensive, continuous education. Not only does such training enhance safety, but it also boosts productivity and operator confidence. Organizations that invest in their operators’ learning journey reap the benefits of a safer and more innovative working environment.
Claim: Continuous and comprehensive training is indispensable for ensuring safety and maximizing efficiency in operating steel wire wrapping machines.