In the sprawling landscape of industrial manufacturing, few components are as ubiquitous and essential as steel coils. These towering rolls of metal are integral to numerous industries, from automotive to construction. However, while their utility is undeniable, the logistics of handling, securing, and transporting them present significant challenges. Central to these logistical issues is the steel coil packing machine, a pivotal tool designed to streamline and secure the packaging process. Despite its vital role, users often encounter a myriad of difficulties that can impede operational efficiency.
As industries continually evolve, so too do the machines and tools they rely upon. The adaptability and efficiency of a steel coil packing machine can make or break a production line’s productivity. Yet, beneath the surface of mechanical precision lies a complex web of potential pitfalls—from maintenance woes to operational hiccups—that can derail even the most meticulously planned operations. Navigating these challenges requires both foresight and a fundamental understanding of the machine’s intricacies.
Claim: Mastery over the common challenges associated with steel coil packing machines is crucial for maintaining seamless industrial operations and maximizing output.
1. What Technical Issues Do Users Face?
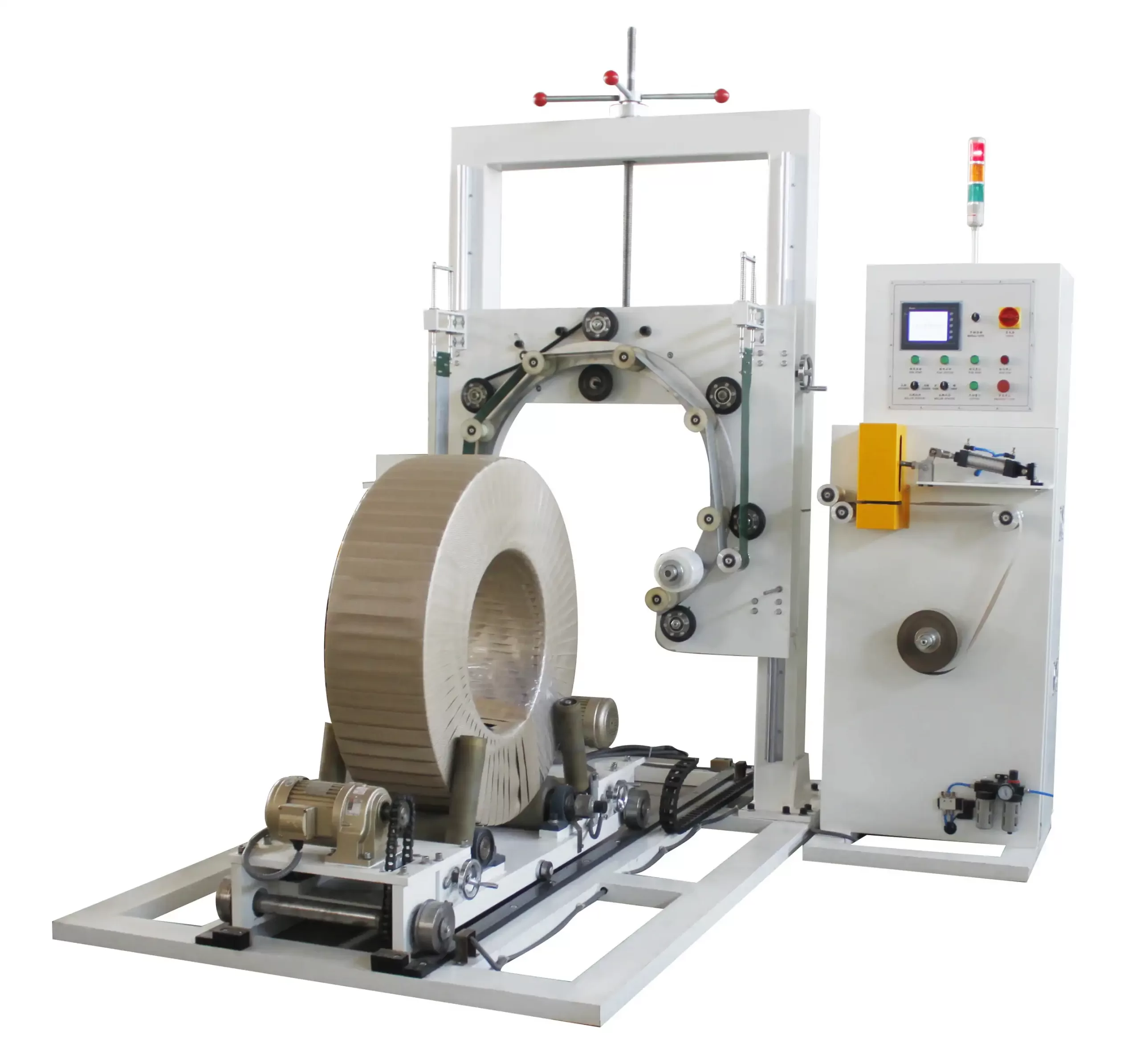
1.1 Understanding Machine Malfunctions
Despite advancements in technology, the complexity of steel coil packing machines means malfunctions are an ever-present risk. These machines operate under high-stress conditions, often leading to wear and tear that can manifest as operational inefficiencies or complete breakdowns. Routine maintenance becomes not just a recommendation but a necessity to mitigate these risks and ensure smooth functioning.
1.2 Operational Efficiency: A Numerical Perspective
According to industry reports, up to 40% of downtime in steel processing plants is attributable to machinery faults. Below is a table illustrating common issues and their frequency:
Issue | Frequency (%) |
---|---|
Belt Misalignment | 25 |
Hydraulic Failures | 35 |
Electrical System Errors | 20 |
Other Mechanical Failures | 20 |
1.3 Insights into Technical Troubleshooting
While technical issues may seem daunting, understanding their root causes can significantly ease troubleshooting. Regular diagnostics can identify minor faults before they escalate. Companies investing in comprehensive training programs for their staff often report a decrease in machine-related downtimes, ensuring a more reliable operation.
1.4 Deep Dive into Preventative Measures
Preventative maintenance is a proactive approach to reducing machine failures. By scheduling regular inspections and replacing worn parts preemptively, companies can extend the lifespan of their machinery. The following table details preventative measures and their effectiveness:
Preventative Measure | Effectiveness (%) |
---|---|
Regular Lubrication | 80 |
Timely Part Replacement | 75 |
Routine Software Updates | 70 |
Comprehensive Staff Training | 85 |
1.5 Two-Fact Statement
True Fact: Implementing a robust maintenance schedule can reduce machine downtime by up to 50%, improving overall production efficiency.
False Fact: Ignoring minor mechanical issues has no long-term impact on the operational lifespan of steel coil packing machines.
2. How Can User Training Minimize Machine Downtime?
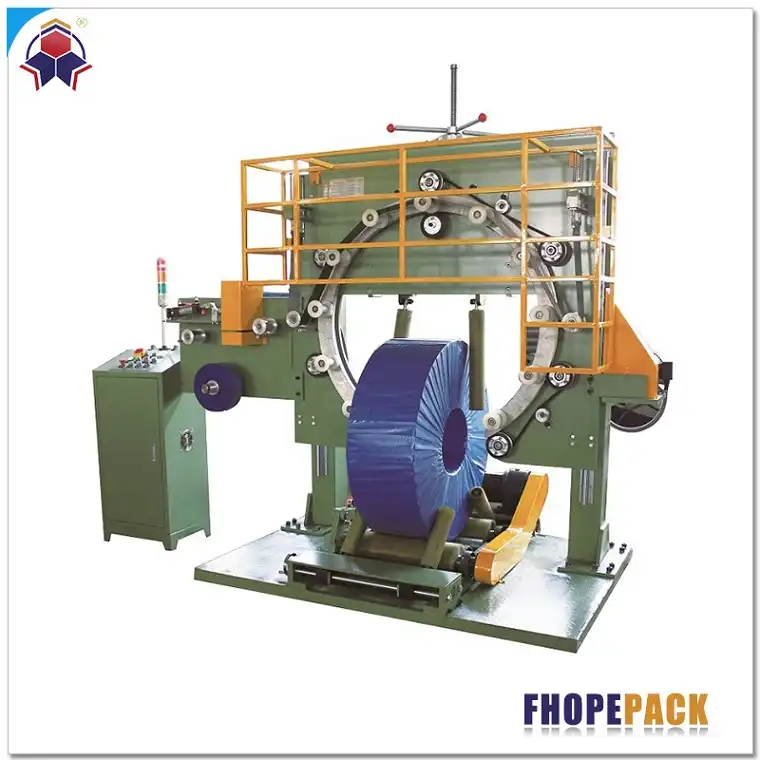
2.1 The Importance of Comprehensive Training Programs
Effective employee training is not merely an option but a crucial component of machine management. Skilled operators are better equipped to handle unexpected malfunctions, reducing downtime and enhancing productivity. Training programs that focus on both theoretical knowledge and practical skills provide employees with the tools needed to maintain optimal machine performance.
2.2 Training Effectiveness: Key Metrics
The success of training programs can be measured through various metrics. Here’s a breakdown of key performance indicators post-training:
Metric | Improvement (%) |
---|---|
Operational Efficiency | 30 |
Downtime Reduction | 25 |
Error Rate | 20 |
Employee Confidence | 40 |
2.3 Bridging Knowledge Gaps Through Continuous Learning
Continuous learning initiatives, including refresher courses and advanced training sessions, are essential for staying ahead of technological advancements. Engaging employees in ongoing education ensures they are up-to-date with new machine features and troubleshooting techniques, ultimately leading to fewer operational disruptions.
2.4 Conclusion: Key Insights and Takeaways
Integrating effective training modules can enhance machine performance and reduce downtime considerably. The following table highlights actionable strategies:
Strategy | Outcome |
---|---|
Advanced Operator Workshops | Enhanced Skillsets |
Refresher Courses | Maintained Competency |
Cross-Training | Increased Flexibility |
Conclusion
Understanding and overcoming the challenges associated with steel coil packing machines is essential for optimizing industrial productivity. From addressing technical malfunctions to implementing strategic training programs, businesses can ensure smoother operations and reduced downtime. Maintaining a proactive stance on machine maintenance and continuous learning will bolster efficiency and reliability across production lines. Claim: By prioritizing machine upkeep and employee expertise, manufacturers can significantly enhance their operational outcomes and maintain a competitive edge in the industry.