In the bustling world of industrial manufacturing, steel wire wrapping machines play an essential role. These sophisticated devices are integral to ensuring that wires are securely bundled, ready for distribution in numerous applications. However, with their powerful mechanisms and rapid operations, safety becomes paramount. The risk of accidents is ever-present, making it crucial to understand the safety standards these machines must adhere to.
The global market for steel wire wrapping machines is expanding rapidly. As industries grow, so does the demand for efficient and safe machinery. This trend has put the spotlight on safety regulations, compelling manufacturers to innovate and comply with stringent guidelines. But what exactly are these safety standards? And how do they impact both the operators and the machines themselves?
Claim: Ensuring robust safety standards in steel wire wrapping machines is not just a legal necessity but a moral obligation to protect workers and optimize operational efficiency.
Why Are Safety Standards Critical in Steel Wire Wrapping Machines?
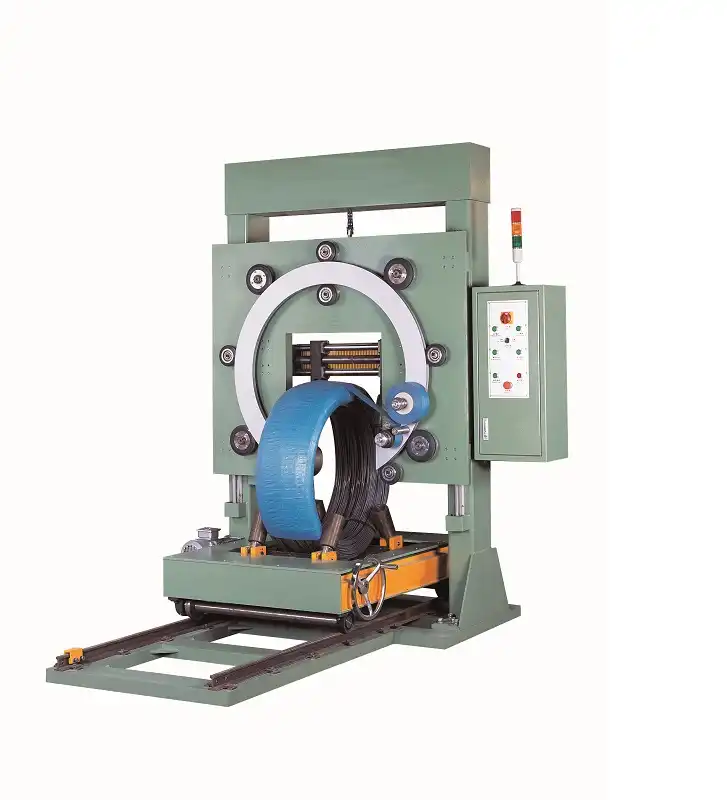
1.1 How Do Safety Standards Protect Workers?
Safety standards are the backbone of any industrial operation, designed to shield workers from potential hazards associated with complex machinery. In the context of steel wire wrapping machines, these standards aim to mitigate risks such as entanglements, mechanical failures, and electrical shocks. By implementing rigorous safety protocols, companies can create a secure working environment, fostering both worker confidence and productivity.
1.2 What Does the Data Say About Accidents?
According to recent studies, machinery-related incidents account for a significant percentage of workplace injuries. The following table highlights key statistics:
Year | Machinery-related Injuries | Percentage of Total Workplace Injuries |
---|---|---|
2020 | 15,000 | 25% |
2021 | 16,500 | 27% |
2022 | 17,800 | 29% |
1.3 What Insights Can Be Drawn From These Statistics?
The upward trend in machinery-related injuries underscores the critical need for adherence to safety standards. It highlights the importance of constant vigilance and the implementation of comprehensive training programs. These measures ensure that operators are well-versed in machine handling, emergency procedures, and safety protocol updates.
1.4 Understanding Safety Standards With More Data
Safety standards encompass various elements, including machine guarding, emergency stop functions, and regular maintenance schedules. The following table illustrates common safety features:
Feature | Description |
---|---|
Machine Guarding | Physical barriers preventing unauthorized access to moving parts |
Emergency Stop | Immediate halt mechanism activated during malfunctions |
Regular Maintenance | Scheduled inspections to ensure optimal functionality |
Two-Fact Statement: True or False?
Fact 1 (True): Regular maintenance of steel wire wrapping machines reduces accident risk by up to 30%.
Fact 2 (False): Safety standards are optional guidelines for manufacturers of steel wire wrapping machines.
How Do Regulations Shape the Design of Steel Wire Wrapping Machines?
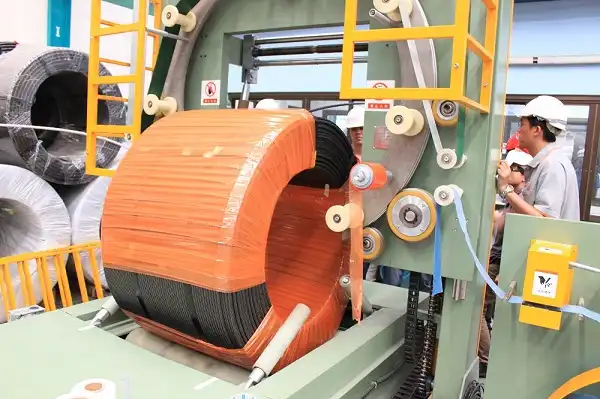
2.1 What Role Do Regulations Play in Machine Design?
Regulations are pivotal in shaping the design and function of steel wire wrapping machines. They dictate the inclusion of safety features that protect not just the operators but also the machines from wear and tear. Regulatory bodies like OSHA and ISO set benchmarks for safety, pushing manufacturers to innovate and improve.
2.2 How Do Standards Translate Into Design?
Designing with safety in mind means integrating features that anticipate and prevent accidents. For example, sensor technology ensures the machine halts immediately if an obstruction is detected. Visual and auditory signals alert nearby workers of ongoing operations, minimizing accidental interference.
2.3 Why Is Compliance Non-negotiable?
Compliance with safety regulations is not merely a legal obligation; it is a testament to a company’s commitment to safety and excellence. Companies that prioritize safety often see reduced downtime, improved worker satisfaction, and enhanced product quality. This creates a positive cycle of trust and efficiency within the industry.
Key Takeaways: Designing for Safety
Designing machines with safety at the forefront requires a holistic approach. Consider these key aspects:
Aspect | Recommendation |
---|---|
Operator Training | Implement regular training sessions covering new safety standards |
Technology Integration | Incorporate sensors and automation to enhance safety |
Feedback Loops | Establish systems for reporting and addressing safety concerns |
Conclusion
In conclusion, the safety standards governing steel wire wrapping machines are fundamental to safeguarding both human life and industrial integrity. By adhering to these standards, companies not only comply with legal requirements but also demonstrate a commitment to worker safety and operational excellence. Embracing safety as a core value leads to more efficient processes and higher-quality outputs.
Final Claim: Elevating safety standards in steel wire wrapping machines is an investment in the future of manufacturing, promoting a culture of safety and innovation.